Does anyone know what ever happened with this?
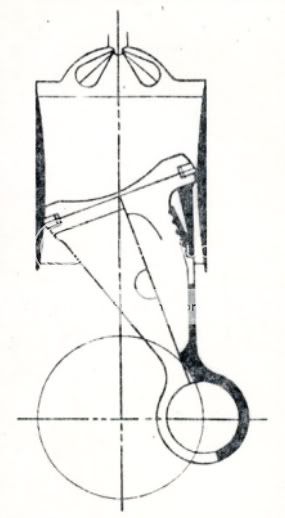
Posted 19 November 2011 - 20:10
Advertisement
Posted 19 November 2011 - 20:43
Posted 19 November 2011 - 21:48
A friend sent me this. He said it was designed in the 70's by some guy named Salzmann.
Does anyone know what ever happened with this?
Posted 20 November 2011 - 07:15
Posted 20 November 2011 - 09:30
Edited by cheapracer, 20 November 2011 - 09:31.
Posted 20 November 2011 - 09:38
A friend sent me this. He said it was designed in the 70's by some guy named Salzmann.
Does anyone know what ever happened with this?
Posted 20 November 2011 - 11:01
Posted 20 November 2011 - 12:13
Yes, a complex shape. A bit like a cooling tower that, seen from one side is normal, but at 90° is cylindrical.The big disadvantage is that grinding a bore that starts circular, goes elliptical, and ends up circular, would be rather tricky to say the least.
Posted 20 November 2011 - 15:33
Yes, a complex shape. A bit like a cooling tower that, seen from one side is normal, but at 90° is cylindrical.
Posted 20 November 2011 - 18:25
Posted 20 November 2011 - 19:18
Posted 20 November 2011 - 20:02
Please forgive my stupidity, but why not just a spherical piston wall? Would work with straight bores...
Posted 20 November 2011 - 21:06
Posted 20 November 2011 - 21:36
That's what's used in the compressor and hydraulic applications. One major problem that stands out is the fact that you'd be limited to a single ring, so oil control would be a challenge. Especially if you had to spray it with oil to compensate for the lack of heat transfer through the skirt.
Posted 20 November 2011 - 22:07
Posted 20 November 2011 - 23:05
Posted 21 November 2011 - 00:46
Posted 21 November 2011 - 03:19
But why would one ever even bother.
Posted 21 November 2011 - 06:59
When I first saw it I thought it might have been used in the experiments with rectangular pistons.
I guess it wasn't. At least the guy put his beer down long enough to draw something half way
interseting.
Advertisement
Posted 21 November 2011 - 07:12
Big marine diesels use crosshead pistons. I don't know why exactly...
Posted 21 November 2011 - 21:14
For production vehicles it has to be reasonably simple to make. And for most motorsport categorys they require round bores so yes it will never take on.Yeah, agreed. Everything that could be good has already been invented, right?
Posted 21 November 2011 - 23:07
Certainly the case with steam engines but rarely (perhaps never) for crosshead diesels.The crosshead engines are usually double acting with a gland around the piston rod to allow both sides of the piston to be working sides.
Posted 22 November 2011 - 03:53
I can understand why it was never heard of. Because it was another dumb idea.
Posted 22 November 2011 - 09:38
Posted 22 November 2011 - 11:22
Posted 22 November 2011 - 11:33
Please forgive my stupidity, but why not just a spherical piston wall? Would work with straight bores...
Edited by Tenmantaylor, 22 November 2011 - 11:37.
Posted 22 November 2011 - 12:27
Working out this constantly varying curvature is actually quite easy in a CAD system but not to manufacture.
Posted 22 November 2011 - 12:55
Probably the biggest mistake I see with "new engines" like this one above is they step outside of common machining practices - there's billions and billions of dollars invested in engine making machines worldwide but you want manufacturers to start all over again?
.... Not going to happen.
Posted 22 November 2011 - 16:55
Posted 22 November 2011 - 17:00
I've never seen anything like that in an engine, but something very similar is often used in hydraulic pumps and motors. In these applications though the cylinders are, well, cylindrical rather than the reverse barrel shape shown here and the head of the piston/rod as well as the ring face is spherical. It works very well in hydraulics as it eliminates the need for a separate drive link but I can't quite grasp the advantage in an engine.
Posted 22 November 2011 - 17:01
I'm not sure that cylinder profile is so difficult to replicate. I've seen it done accidentally lots of times.
Posted 22 November 2011 - 18:15
Posted 22 November 2011 - 21:00
With modern CNC machinery it would be a doddle to make. Modern injection moulding tools don't even need polishing after they come out of the machining centre.
Posted 22 November 2011 - 23:14
Conversely there have been many ideas that deserved to win through but didn't simply through lack of effort. Why? - usually lack of vision or conservatism from potential backers - sometimes deliberate supression by those who stand to lose.On a much smaller scale I always find it fascinating when one has to choose when to drop an architecture (or idea) during the development process, in favour of some other, usually more conservative, path. There are innovative ideas where the concentrated application of effort has resulted in success,
Posted 22 November 2011 - 23:17
Cylinder bores would require an additional process or two.With modern CNC machinery it would be a doddle to make. Modern injection moulding tools don't even need polishing after they come out of the machining centre.
Posted 22 November 2011 - 23:35
The rotary engine after 50 + years really is still an expensive oddity. It is smooth and reasonably powerfull but not very economical and has frequent and high service costs.The Darwinian evolutionary principles such as survival of the fittest, natural selection, elimination of the weak, etc. apply to engine design as much as biological systems. Fortunately, evolutionary abnormalities like this Salzman concept are quickly eliminated through natural selection. With evolution of engine design, just as in evolution of biological species, the only developments that become successful are those that are better overall than the status quo. While the idea of a one-piece piston/rod would appear to have merit in principle, in practice the concept requires too many other compromises to be of any benefit.
Occasionally however, there is the rare example of an engine concept (like the Wankel rotary) that would seem to make no engineering sense, yet ends up being somewhat successful commercially due to relentless development effort. Ironically, the Wankel has a one piece "piston and rod".
Posted 23 November 2011 - 00:54
With modern CNC machinery it would be a doddle to make.
Posted 23 November 2011 - 00:56
Posted 23 November 2011 - 02:40
Advertisement
Posted 23 November 2011 - 03:54
I suppose two architectures spring to mind -swash plate engines
In one case hardly anybody has put much money into them,
Posted 23 November 2011 - 04:07
Posted 23 November 2011 - 06:44
Posted 23 November 2011 - 07:37
The Queensland Split Cycle had radially oriented pistons actuated by a kind of rolling cam mechanism.
Posted 23 November 2011 - 08:00
It never realy produced enough power to run itself . most demos were powered by a suply of compressed air..The Queensland Split Cycle had radially oriented pistons actuated by a kind of rolling cam mechanism.
Posted 23 November 2011 - 10:21
This design might make sense in cheap 2 stroke model engines which could be simply cast (not requiring machining), and having less parts would keep the cost down and result in an engine with less things to go wrong.
Has this been built yet ?
Posted 23 November 2011 - 14:38
It never realy produced enough power to run itself . most demos were powered by a suply of compressed air..
A french testing house eventually came up with a figure of 1% eficiency.
Posted 24 November 2011 - 01:14
Posted 24 November 2011 - 01:55
On a much smaller scale I always find it fascinating when one has to choose when to drop an architecture (or idea) during the development process, in favour of some other, usually more conservative, path. There are innovative ideas where the concentrated application of effort has resulted in success, and a successful innovator must have more of those under his belt than the ideas that never see the light of day despite equivalent effort. I wish I had that sort of brain, but I don't.
Posted 24 November 2011 - 10:31
Posted 24 November 2011 - 11:55
I would have thought that sintering for producing rocker arms was a more important development.
Almost all Leyland engines in the 60/70's had them and few needed any bushes to run on the shafts.
If I remember, the steel pressed versions were two piece riveted, or welded together.